木材撕碎机产量下降原因分析
木材撕碎机是一种将完整木材加工成不同尺寸木片的专业机械。该机器内部包含刀板、刀片、锤片和筛网。处理后的物料将从机器底部排出。我们生产不同型号的木材粉碎机。而且它们的产量不同,可以生产不同尺寸的木片。我们还可以在上面添加高架子和轮子 木材粉碎机 对于我们的客户来说,这使他们可以轻松移动机器。
木材撕碎机产量下降的原因
木材加工客户的加工能力大不如前,大致有两个原因。一方面, 木材粉碎机 使用时间较长,未及时维护和保养。另一方面,木材撕碎机可能会因为操作不当而导致机器刀片磨损非常厉害。针对这个棘手的问题,舒利机械厂简单为您提出了一些解决方案。然而,对于木材破碎机在使用过程中,合理的维护也是必不可少的问题之一。
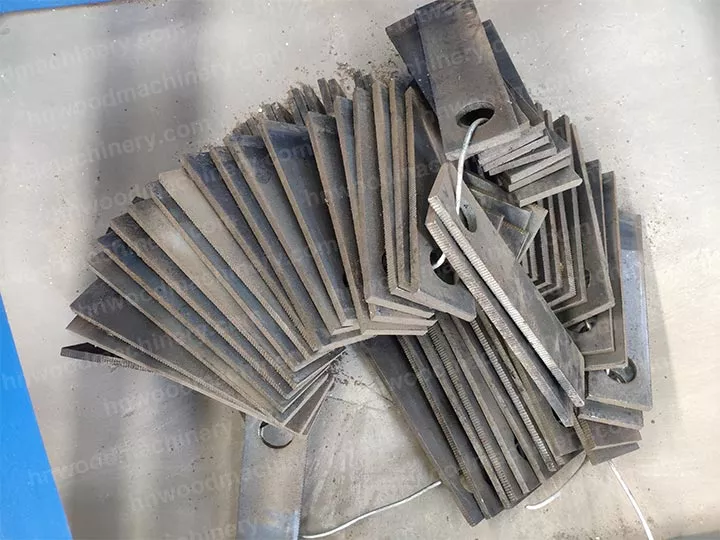
木材撕碎机出现故障的具体原因及解决办法
1、木材破碎机产量突然下降。
原因:一是由于喂料停止或减少。另一种是因为输送管道被堵塞。
解决办法是:检查并调整送料速度,做到送料均匀。或者停车检查排除管道堵塞部分,然后清洗即可解决问题。
2、木材破碎机产量逐渐下降。
原因:可能是重要工作部件间隙增大。
解决方法:首先调整木磨机主机筛网齿轮间隙,然后调整引风机风量。
3、木材破碎设备产量大幅下降。
原因:这可能是因为木材破碎机刀具磨损比较强。
解决方案:这需要重新研磨工具或更换新工具。
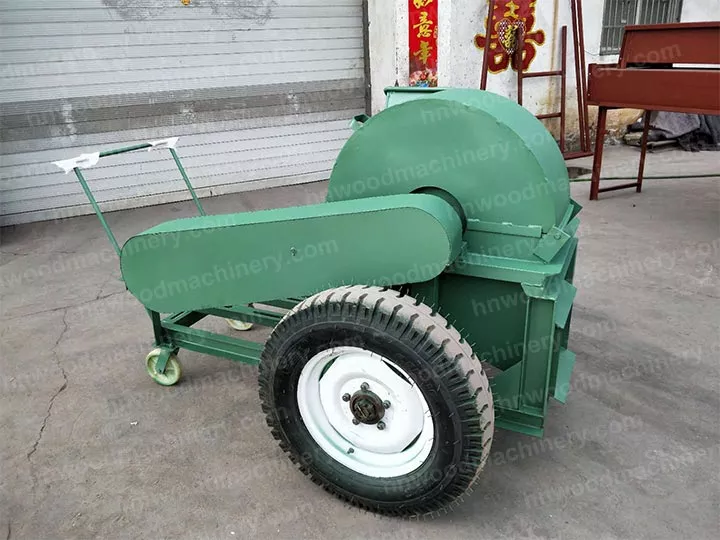
木材破碎机的保养方法
1、经常使用机器,进行保养尤为重要。
2、应制定检查计划,及时排除机器故障,并对机器进行清理。每天加工结束后,检查各部分螺丝没有松动的情况以及牙爪、筛网等易损件的磨损情况。
3、经常加注油脂。我们需要及时给机器的轴承添加润滑油,这样我们的机器才能保持平稳运转。
4、加工的数量和频率可以看说明书,具体应用可以根据每天的生产量来确定。
5、精心选择需要粉碎的原料。严禁将铜、铁、铅等金属件及较大石块等杂物混入破碎腔内。
6、对于机器的转速,不要随意调整,一般允许与7%-9%的额定转速不同。
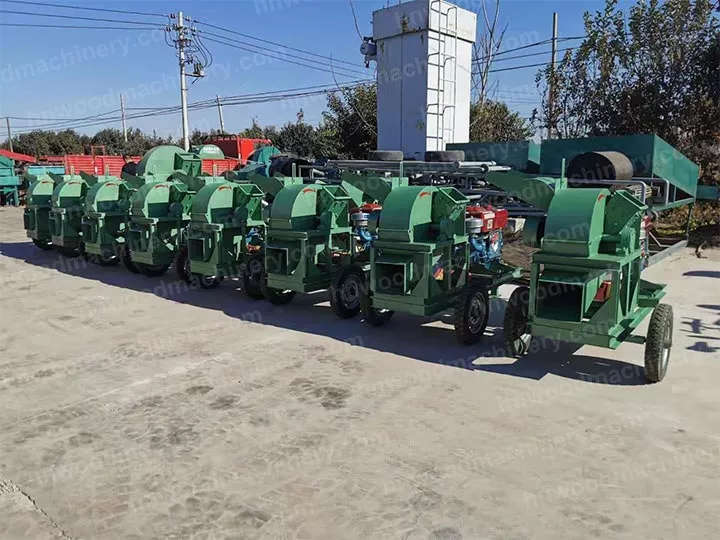